The lifespan of a polyurethane (PU) foam roof panel typically ranges from 25 to 40 years, depending on the type of panel and the environmental conditions at the installation site.
LUSEN, a leading manufacturer of high-quality PU panels, has developed indigenous technologies tailored to suit various climatic conditions, particularly in Asia and Europe. LUSEN panels are designed to provide exceptional durability and performance, ensuring a longer lifespan even under challenging conditions.
Especially in Asian climates, LUSEN panels have demonstrated outstanding longevity, making them an excellent choice for roofing applications. By combining advanced materials and innovative manufacturing processes, LUSEN ensures that its products meet the highest standards of quality and reliability.
Key Features of LUSEN Panels
1. Superior Insulation Performance
High Thermal Resistance: LUSEN panels are designed with a core made from high-quality polyurethane foam, offering excellent thermal insulation properties. This results in significant energy savings and improved indoor comfort.
Acoustic Insulation: The dense foam core also provides superior soundproofing, reducing noise transmission and enhancing the acoustic environment.
2. Durability and Longevity
Corrosion Resistance: The outer layers of LUSEN panels are often made from corrosion-resistant materials such as aluminum or coated steel, ensuring long-term durability even in harsh environments.
Weather Resistance: Designed to withstand extreme weather conditions, including heavy rain, strong winds, and temperature fluctuations, LUSEN panels provide reliable performance over their lifespan.
3. Fire Safety Compliance
Enhanced Fire Resistance: Many LUSEN panels meet stringent fire safety standards, incorporating fire-retardant additives into the foam core. Some configurations achieve high fire ratings, making them suitable for various building applications.
4. Lightweight yet Strong
High Strength-to-Weight Ratio: Despite their lightweight design, LUSEN panels offer exceptional structural strength, making them easy to handle and install while maintaining robust performance.
5. Customizable and Versatile
Wide Range of Applications: Suitable for a variety of applications, including roofs, walls, ceilings, and cold storage facilities. LUSEN panels can be customized in terms of size, color, and finish to meet specific project requirements.
Easy Installation: Featuring interlocking systems that simplify installation processes, reducing labor costs and project timelines.
6. Environmental Friendliness
Sustainable Materials: LUSEN panels are manufactured using environmentally friendly materials and processes, contributing to sustainable building practices.
Energy Efficiency: Their excellent insulation properties help reduce energy consumption, leading to lower carbon emissions and a smaller environmental footprint.
7. Adaptability to Local Conditions
Tailored Solutions: Developed with indigenous technologies, LUSEN panels are specifically designed to suit the climatic conditions and usage requirements of Asian and European markets. They excel in adapting to diverse environmental challenges, ensuring optimal performance in different regions.
Conclusion
LUSEN panels combine advanced technology, superior materials, and tailored design to deliver high-performance solutions for a wide range of construction needs. Whether for residential, commercial, or industrial projects, LUSEN panels offer reliability, efficiency, and longevity, making them an excellent choice for builders and architects.
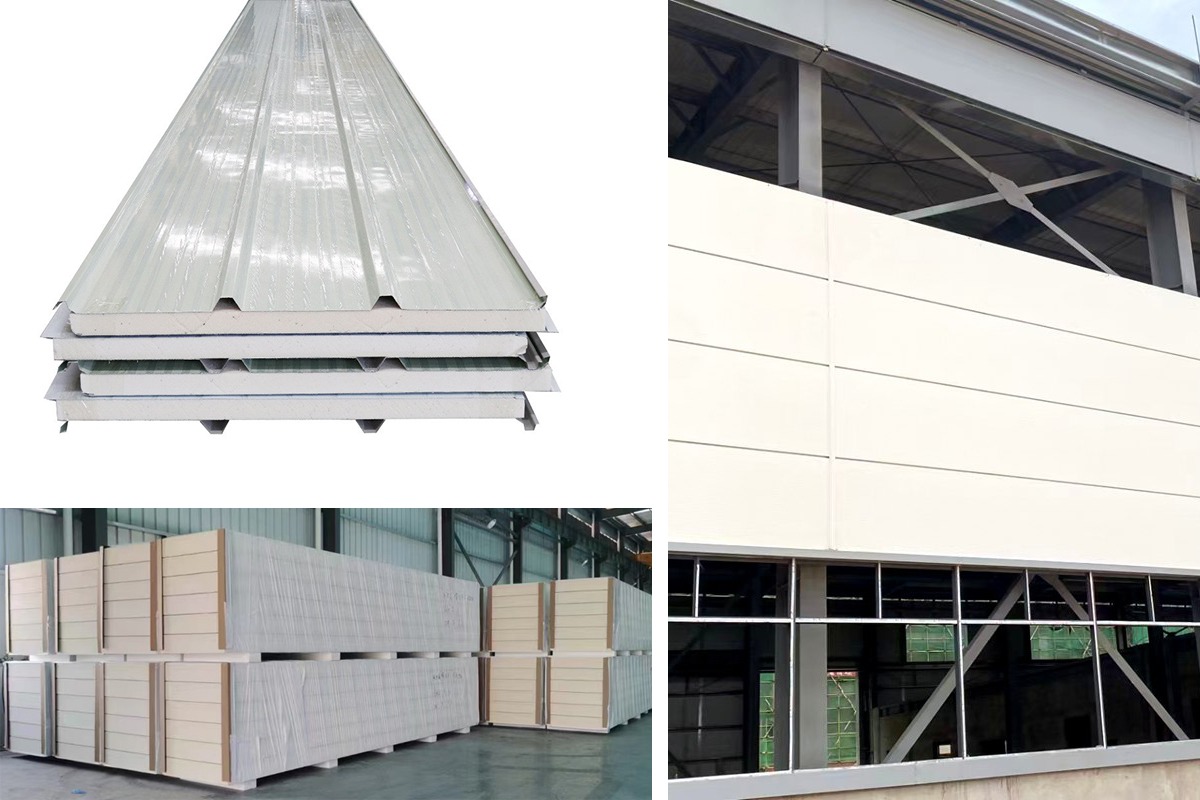