Sandwich panels: the “filled cookie” of the architectural world, making your building “sweet” to the core.
In the world of construction, there exists a remarkable material that closely resembles our beloved sandwich cookie: crisp biscuits on the outside and a sweet cream filling in between. Just as a bite of a cookie brings surprise and satisfaction, this is exactly what sandwich panels do for buildings. Despite their unassuming appearance, they conceal a powerful secret weapon that makes buildings “sweet” down to their core. They not only provide a layer of “thermal insulation” to resist harsh winters and scorching summers but also transform the construction process into something easy and quick, akin to an engaging “puzzle show” on a construction site. More marvelously, it comes with an “environmental halo,” being entirely recyclable from top to bottom, ensuring that while buildings remain “sweet,” they also sport a “green figure.”
Let’s follow LUSEN as we delve into the magical world of sandwich panels and explore how its “sandwich magic” ushers in a sweet revolution for buildings.
1. Pioneer in Energy Conservation
Sandwich panels stand out particularly in building energy efficiency. The internal thermal insulation materials, such as polyurethane foam and rock wool, effectively prevent heat transfer, keeping interiors warm during winter and cool in summer. This outstanding insulating performance significantly reduces reliance on air conditioning and heating systems, lowering energy consumption and enhancing building efficiency. For instance, using sandwich panels for exterior walls and roofs in cold regions can noticeably reduce indoor heat loss, stabilizing indoor temperatures and decreasing the frequency and intensity of heating equipment use.
2. Practitioner of Environmental Sustainability
The environmental friendliness of sandwich panels manifests in various ways. Firstly, many of the raw materials used in production are renewable, like recycled PET bottle foils and light wood. Utilizing these materials reduces natural resource extraction and environmental damage. Secondly, sandwich panels generate less waste during use, with most materials being recyclable. For example, both the metal facings and core materials of metal-faced sandwich panels can be processed and reused for other products. Additionally, the lightweight nature of sandwich panels decreases transportation costs and carbon emissions during construction. Throughout a building's lifecycle, the environmental advantages of sandwich panels become increasingly evident, providing robust support for green buildings and sustainable development.
3. Innovator in Construction Convenience
The construction process with sandwich panels is simple and swift, greatly improving construction efficiency. Since they are prefabricated panels, installation involves merely assembling and securing them according to design requirements, without complex on-site processing. This method shortens construction time, reduces costs, and minimizes noise and dust pollution. In high-rise, public, and residential buildings, the use of sandwich panels enhances construction efficiency and safety. For example, in prefabricated modular structures, sandwich panels serve as components of precast concrete insulated exterior walls, enabling prefabrication and assembly-style construction. This approach integrates design, production, and construction, promoting industrialized construction and maximizing the energy-saving, environmental protection, and lifecycle value of building products.
4. Inspiration for Design Innovation
The diverse material options and structural characteristics of sandwich panels offer abundant room for architectural innovation. Facing materials can be metal, polymers, or fiber-reinforced composites, while core materials may include foamed plastics, honeycomb structures, or lightweight woods. This versatile material combination allows sandwich panels to meet different architectural styles and functional needs. Architects can select facing materials with varying colors, textures, and finishes to create unique architectural aesthetics. Moreover, the high strength and lightweight properties of sandwich panels provide more possibilities for structural design. For example, using high-strength sandwich panels as structural materials in large-span spaces enables greater spatial spans, creating expansive indoor areas.
5. Limitless Possibilities for Future Development
As technology advances and market demand grows, the application prospects of sandwich panels in the construction industry will broaden. On one hand, developments in material science will endow sandwich panels with superior performance. For example, nanotechnology can enhance the core material's strength and rigidity while reducing overall weight, improving structural efficiency. On the other hand, the development of recyclable or biodegradable core materials will further improve the environmental performance of sandwich panels, minimizing environmental impact. Furthermore, the application of sandwich panels in smart buildings will expand. Integrating intelligent technologies, sandwich panels can achieve functions like temperature regulation and light control, supporting the development of smart buildings.
In summary, the application of sandwich panels in construction not only elevates building performance and quality but also provides strong support for the sustainable development of the construction industry. Their advantages in energy conservation, environmental sustainability, construction convenience, and design innovation make them an indispensable material in modern architecture. As technology continuously innovates and markets evolve, sandwich panels will play an even more critical role in the construction field, contributing to the creation of a more beautiful and sustainable living environment for humanity.
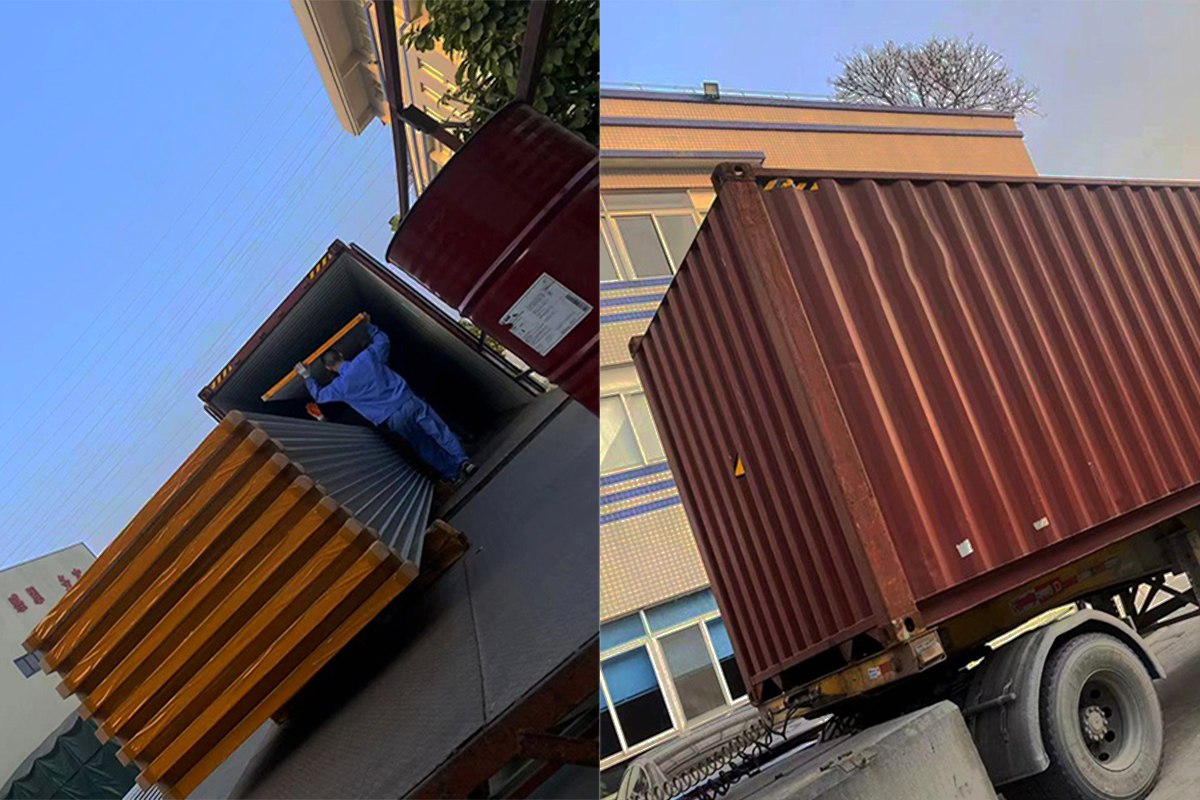